The port of Ancona is the primary Italian port for international vehicle and passenger traffic, with over 1.5 million passengers and 200,000 articulated lorries each year. It is also first in the Adriatic for cargo flows. Dock 22 is located in the container handling area.
THE PROBLEM
Self-propelled cranes with a static working load of 30.00 tons/sq. m operate in the service area. Heavy machinery passing over paving with a subgrade consisting of soil with poor mechanical properties and voids led to subsidence of the pavement: damage, especially depressions, which, if aggravated beyond a certain point, would have prevented the cranes from functioning properly, consequently making the dock unusable.
Customer needs
It was not possible to plan for prolonged work stoppages, so the intervention needed to be quick and minimize the impact on port activities. It also had to fully protect the safety of personnel and guarantee long-term effectiveness of the consolidation work.
Why the Port of Ancona chose Uretek:
- Speed
Careful planning and programming of the times allowed the work to be completed in just 11 days; - Non-invasive
The intervention proposed by Uretek did not require removal of the road structure, and it did not dirty the area or produce waste; - Localized work
The Uretek team delimited the work area, allowing regular port activities to continue; - Continuous monitoring of the work
Both during and after the intervention, the activities were subject to control by highly qualified personnel using advanced laser technology; - Exclusive Uretek technology
The intervention involved the injection of Uretek Geoplus® resin. With its high swelling pressure, it compacts the soil and stabilizes structures; - Respect for the environment
Above-ground mixing of the Uretek® resin creates a final inert product that does not release solvents into the soil or possible water tables in the area.
THE SOLUTION
As the Uretek Geoplus® resin expands, it filled the voids in the soil, compacting the surrounding solid volume and improving its mechanical and hydraulic properties. We then verified the success of the work, making 10 comparative penetration tests before and after the intervention. We stabilized 568 sq. m of paving in 11 days without the need for accessory work or demolition.
THE INTERVENTION IN DETAIL
Monitoring
We monitored the quay surface constantly using laser instrumentation (accuracy ±1.0 mm), which made it possible to record a lift in the pavement up to a maximum of 2 mm.
Penetration tests
We verified the success of the intervention by making 10 comparative dynamic penetration tests (5 pairs of tests before and after the intervention), which showed an enhancement in mechanical properties in the volumes of soil treated with injections. At some points in the pre-injection vertical test holes, the presence of granular material made it necessary to create a pilot hole. In addition to verifying the outcome of the treatment during the work, the tests made it possible to check the quantities to be injected with respect to the design forecasts.
Uretek Seismic Test
During the work, we applied a geophysical method to assess the rigidity of the ground beneath the foundations. The Uretek Seismic Test European patent consists of a system of geophysical tests to investigate layers in the ground, starting from ground level, without being influenced by the more rigid surface layers, known as ‘ghost layers’.
We made a seismic spread on the road paving, both before and following the injections. The geophones deployed over the paving were excited by the energy produced by a seismic source, allowing us to detect the transmission speed of VS shear waves in the layer under the foundation. The increase in VS shear wave velocity demonstrated the improvement of the treated soil.
Observations
The graph below shows a comparison, with the same material injected at each point, between resins with different expansion characteristics..
The Uretek Geoplus® resin develops swelling pressures on the order of 10,000 kPa, thickening the soil at a distance twice what is possible with a material with a pressure of 1000 kPa.
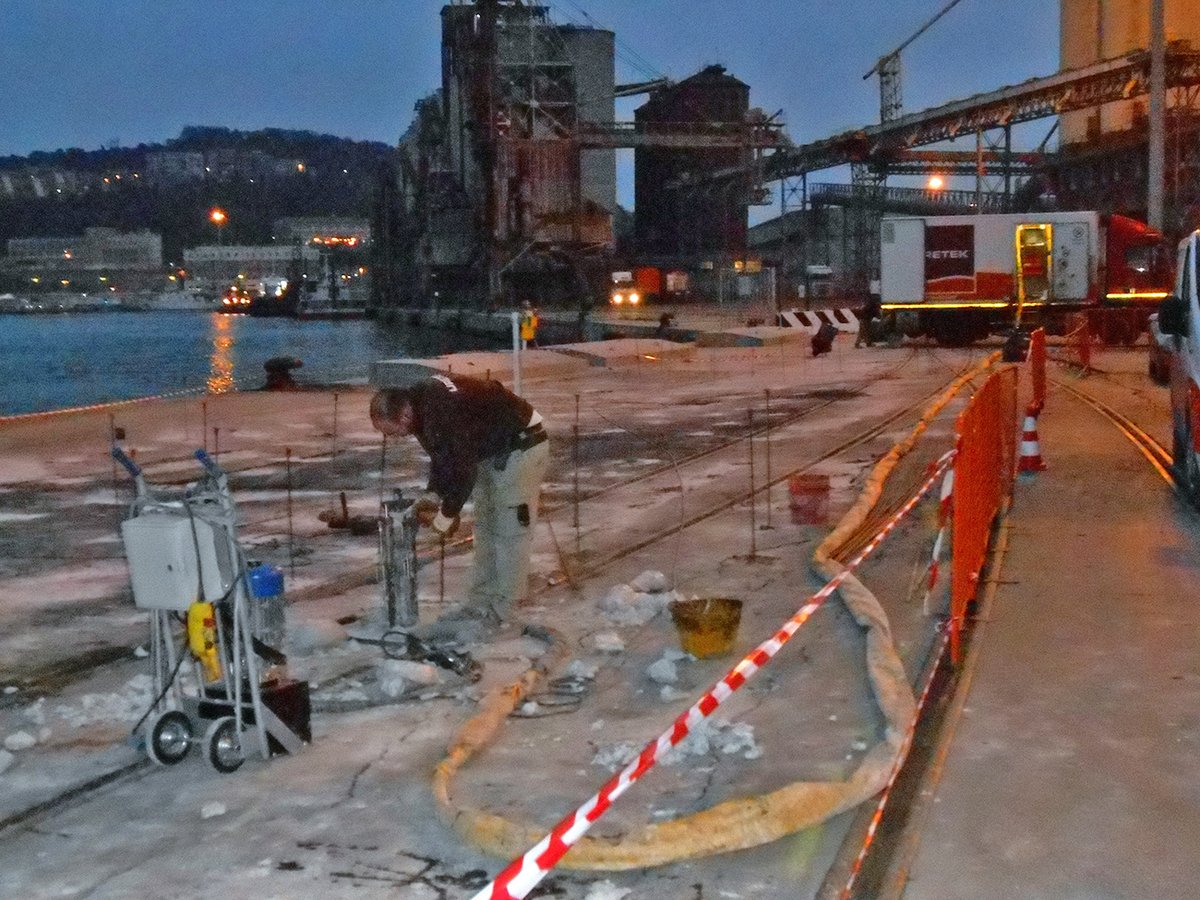
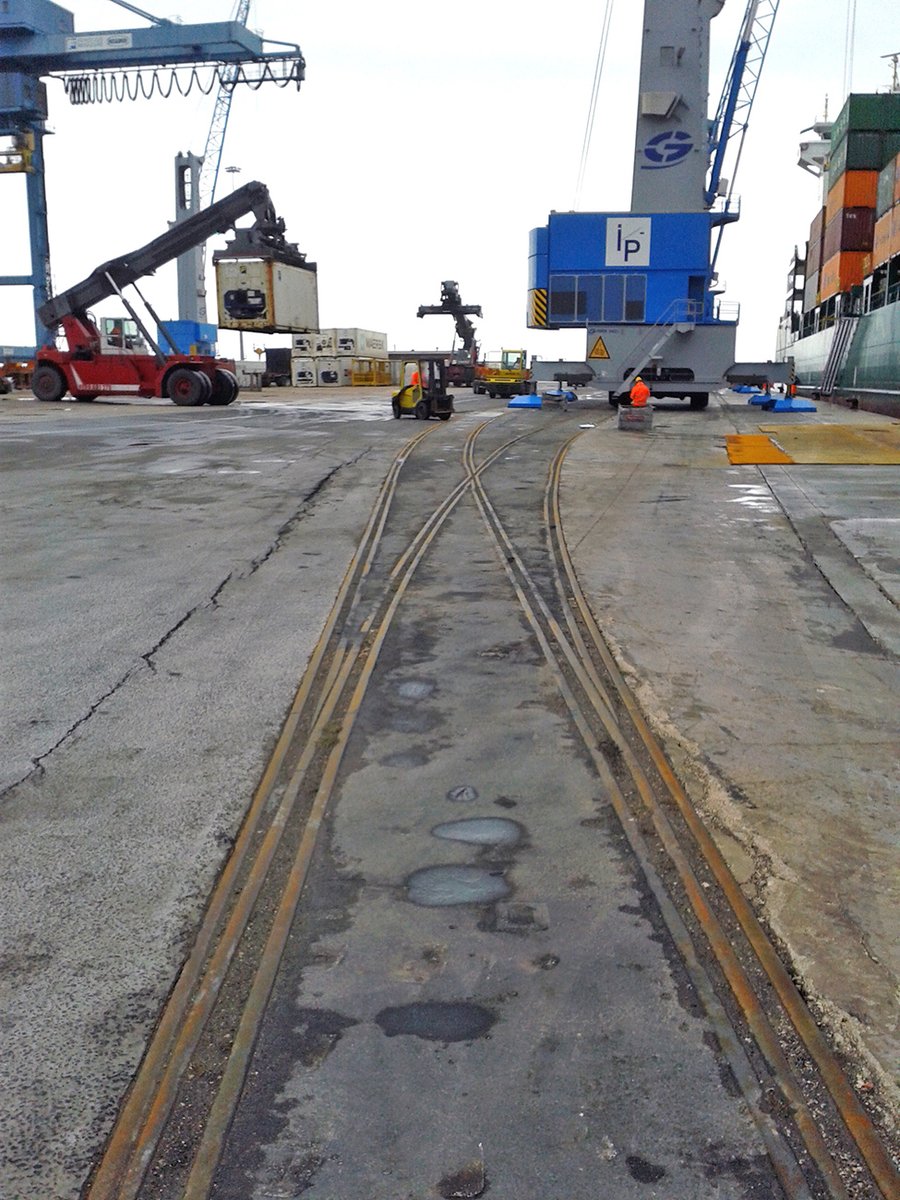
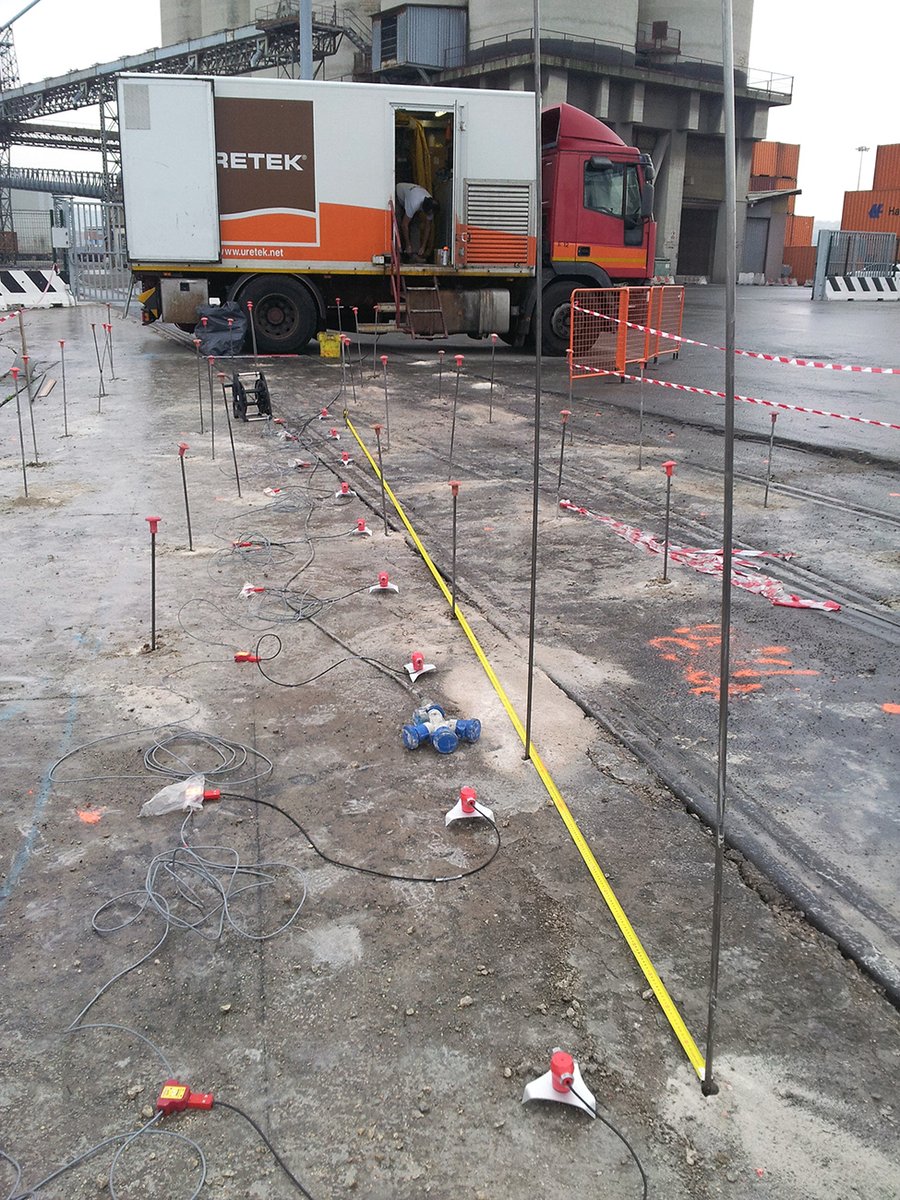
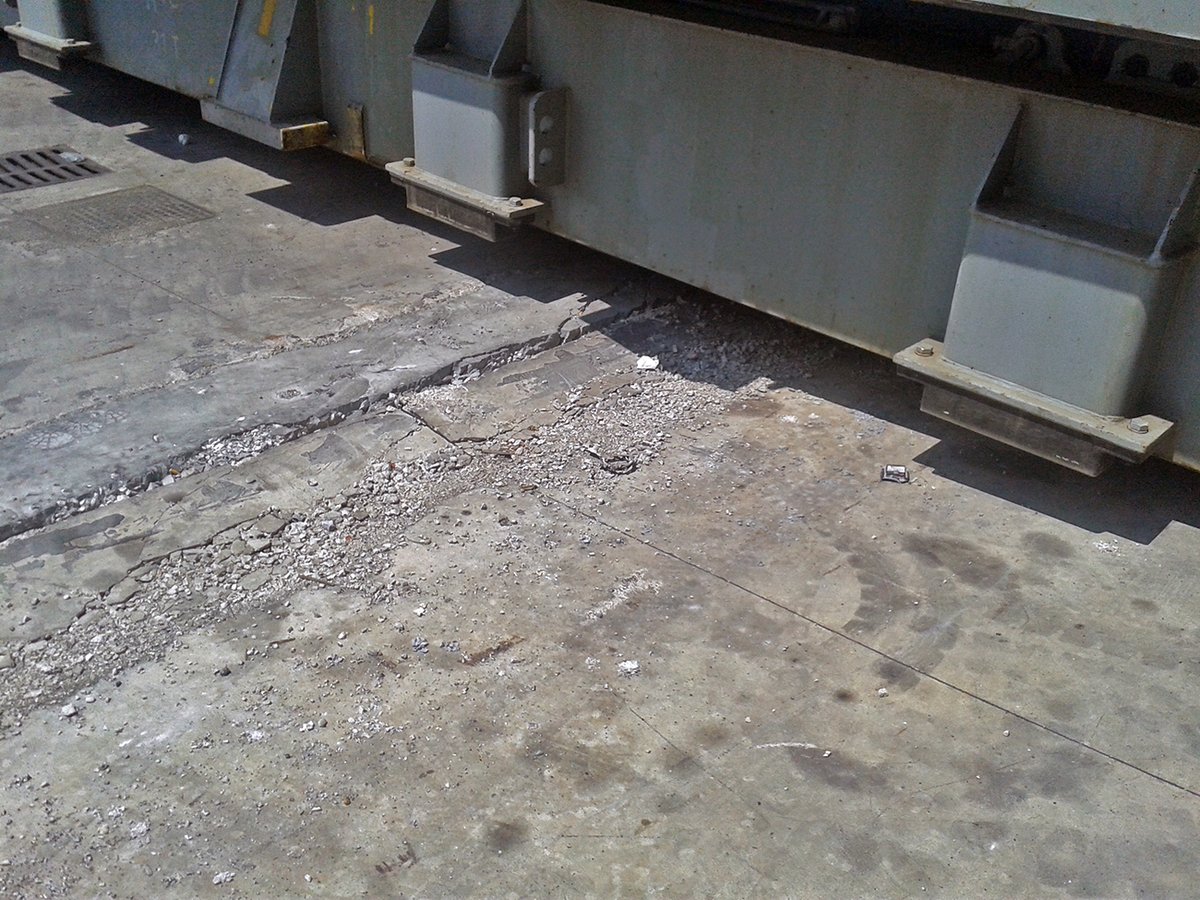
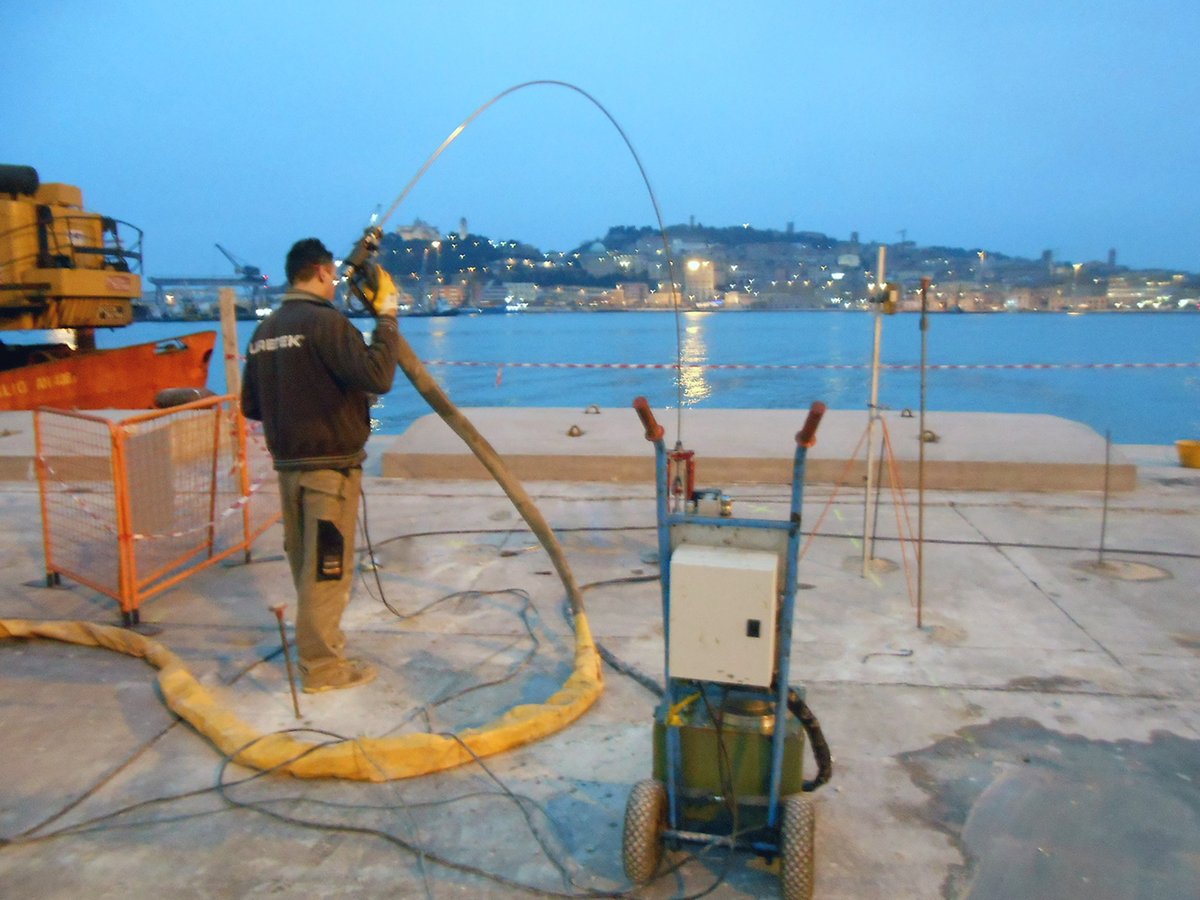
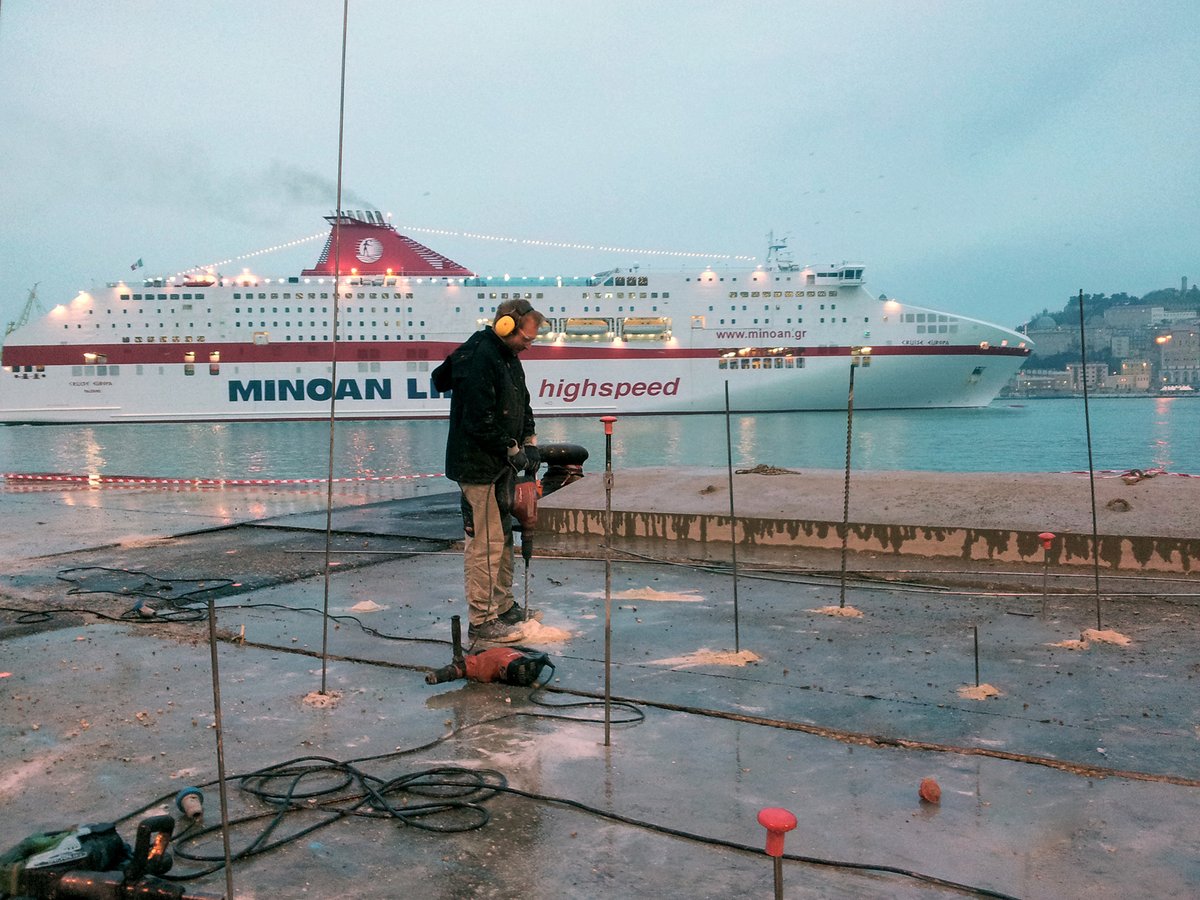