Line A of the Rome Metro, characterized by an orange colour, was the second line to be built in the capital. Today it has 27 stations and a length of 18.425 km. The object of our intervention was the tunnel between the Roma Termini and Colli Albani stations.
THE PROBLEM
Widespread infiltration had caused degradation detectable in both the reinforced concrete cladding in the tunnels and in the technical and system equipment of the line, as well as the finishings and station systems.
Customer needs
It was necessary to quickly correct and consolidate all structures to guarantee the safety of the service without interrupting regular train traffic.
Why the Uretek solution was chosen:
- Speed
Careful planning and programming of the times allowed the work to be completed in just a few days; - Non-invasive
The intervention proposed by Uretek did not require excavations or masonry work, and it did not dirty the area or produce waste; - Localized work
The Uretek team delimited the work area, allowing regular work activities to continue; - Continuous monitoring of the work
Both during and after the intervention, the activities were subject to control by highly qualified personnel using advanced laser technology; - Application of the exclusive Uretek Deep Injections® technology
A special expanding resin with high swelling pressure is injected into the soil, compacting it and stabilizing the structures; - Respect for the environment
Above-ground mixing of the Uretek® resin creates a final inert product that does not release solvents into the soil or possible water tables in the area. - Uretek is qualified in the special category LOC001 (SQ011 QUALIFICATION SYSTEM ‘CIVIL WORKS AT THE RAILWAY SITE’) and by SNFC for know-how in the railway sector.
THE SOLUTION
We filled the voids in the prefabricated concrete ashlar cladding and the soil, injecting the special Uretek Geoplus® resin. This created barriers designed to block the continuity of the large voids running along and across the tunnel, allowing for subsequent injections of cement without it spreading. We treated two partitions, each consisting of three consecutive rings of prefabricated ashlar, called A B C D E F. The goal was achieved in both sectors in question.
THE INTERVENTION IN DETAIL
The initial situation
The section treated in the intervention had two different tunnels with cladding in rings of prefabricated concrete ashlar. Each ring measured 1 metre along the tunnel axis. Towards the interior of the tunnel, the prefabricated ashlar had intermediate and perimeter ribs, and the cladding surface was moulded into a recessed profile. The construction method did not involve the insertion of seals along the edges between the different ashlar elements; rather, waterproofing was entrusted to interposing a layer of mastic asphalt between the elements. The infiltration paths were generally located near the joints between the ashlar elements and the holes for the tightening bolts. The results of the analysis campaign made in December 1999 and January 2000 (coring, georadar, Lugeon tests, etc.) showed a high coefficient of permeability. The probable causes were infiltration, a general detachment of the concrete cladding from the soil behind it, and the presence of voids to a thickness of about 20 cm. Since the continuous voids run both along and across the tunnel, we supposed that the ‘thickness of extra excavation’ had not been filled adequately.
Operational phases
Previous work to contain the infiltration had generally been limited to plugs from within (sealing and plastering the joints with various materials) and/or the channelling of percolated water present in the cladding (installing channels and joint covers), which did not lead to appreciable results with respect to a general long-lasting renovation.
After transferring all the equipment and resin drums from the Uretek truck to the rail wagon and building suitable scaffolding to safely lift a worker to the vault, we injected the resin into the intrados of the ashlar along three quarters of the circumference of the rings. About 42 sq. m of each partition was treated.
Working at night between 11 p.m. and 4 a.m., we were able to treat one partition per night. To make the injections, we used holes made previously by the general company, suitably equipped with copper tubes (Ø 12 mm) sealed to the concrete ashlar.
We optimized the injection sequence to reach the goal: creating barriers that interrupted the large voids in the intrados of the concrete cladding running along the tunnel.
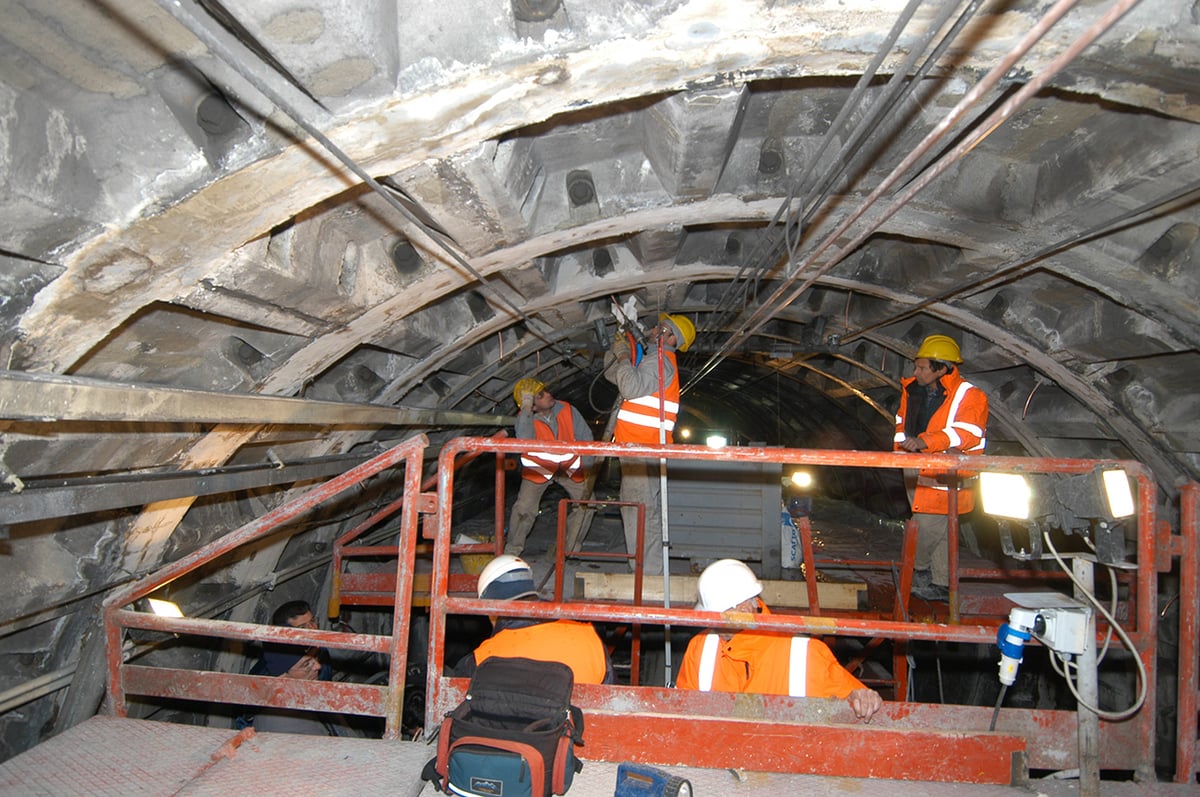
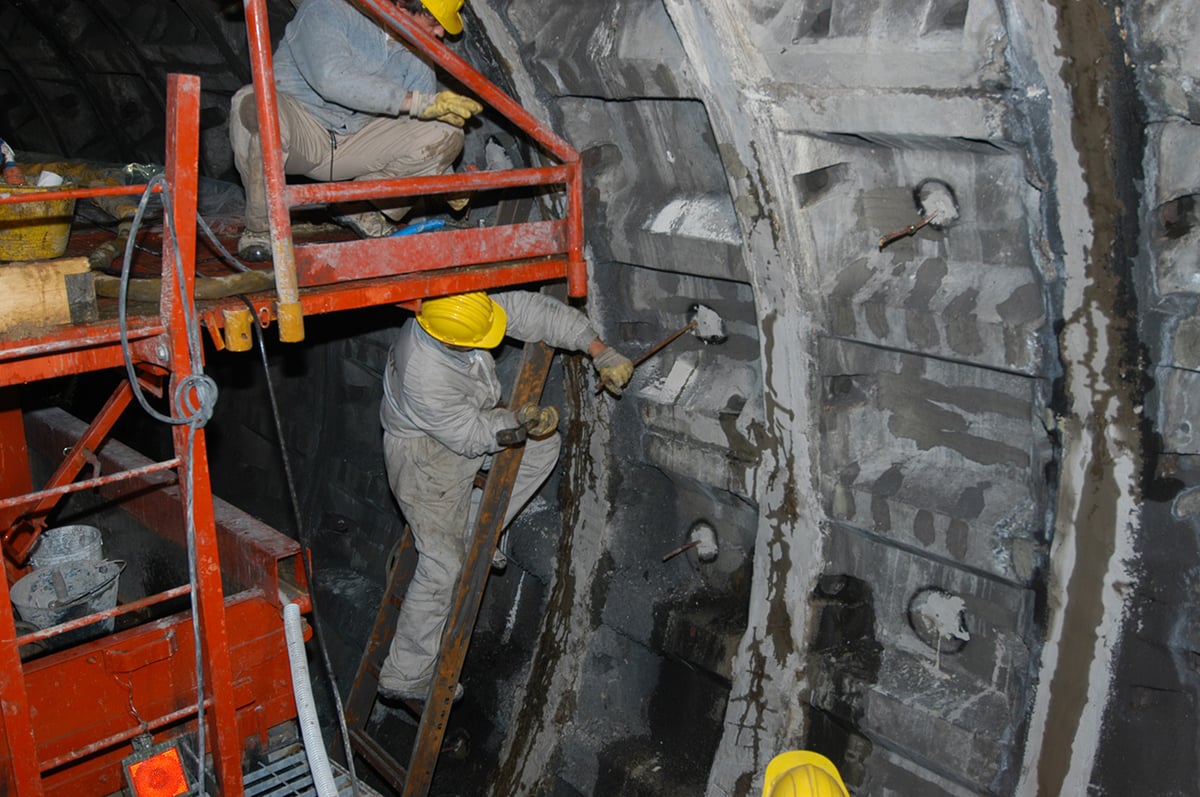
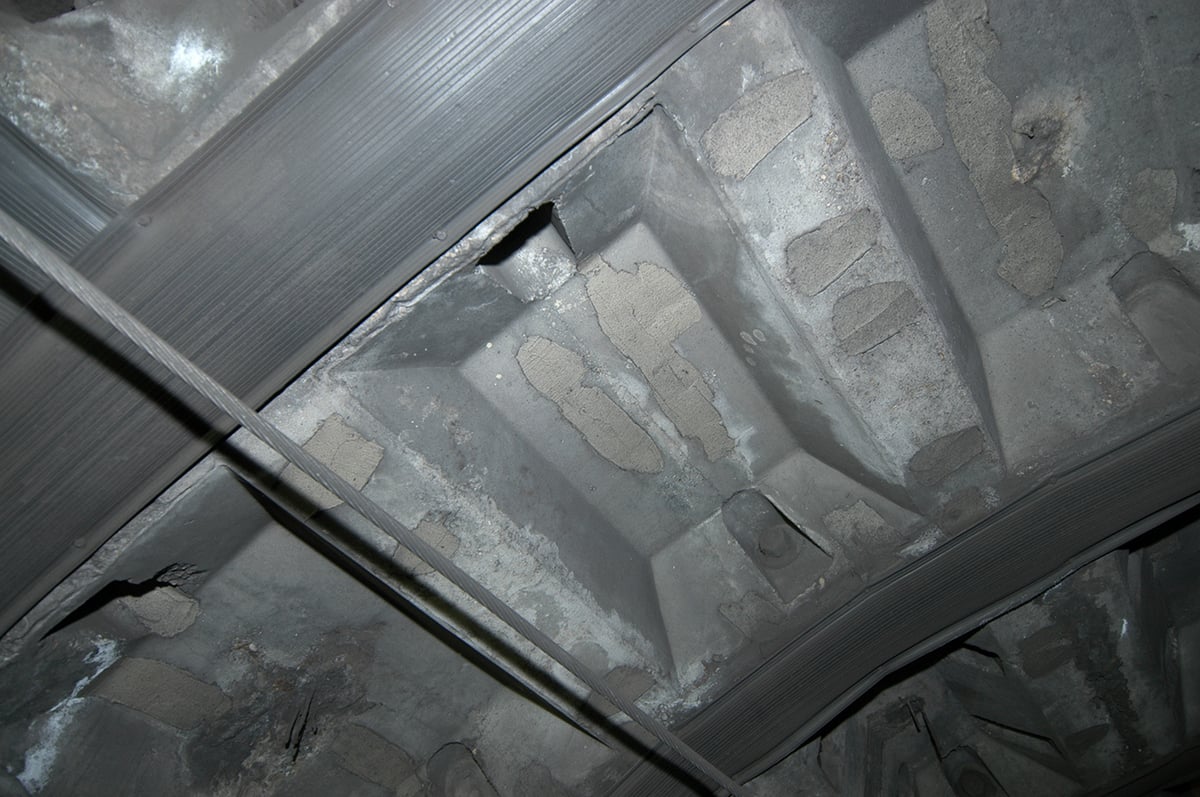
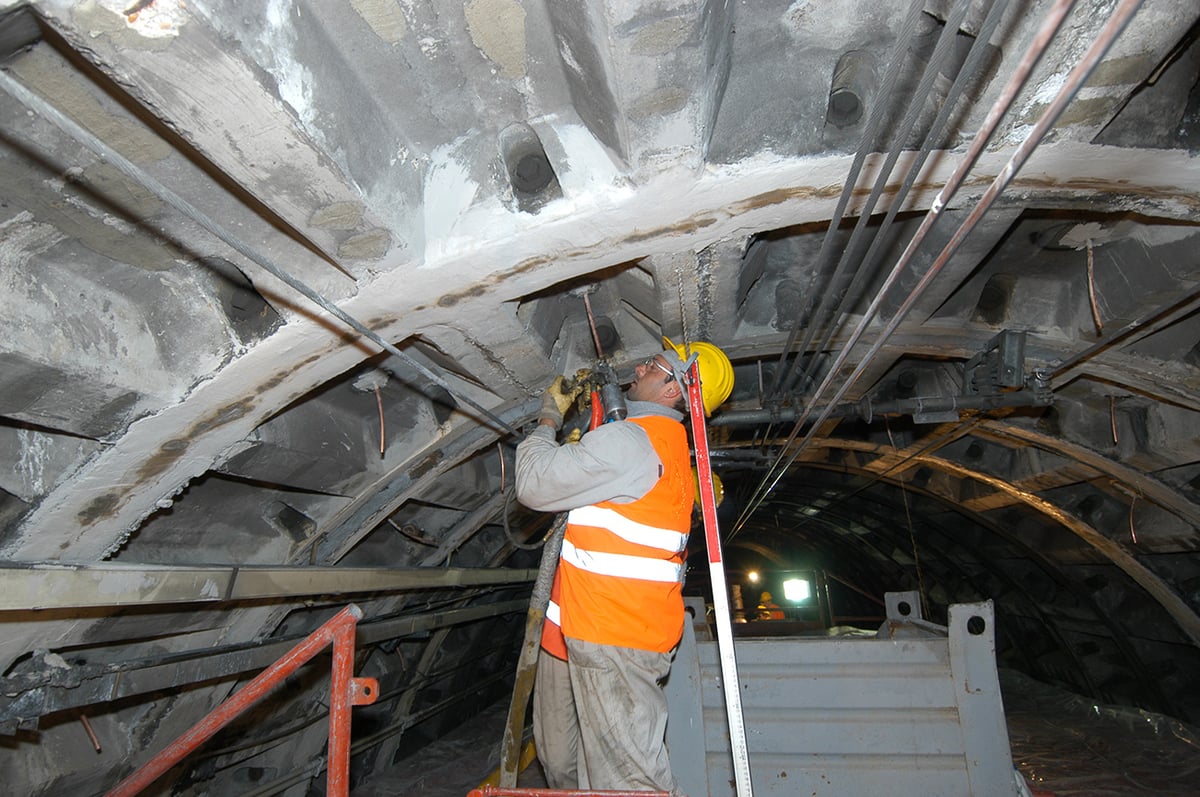
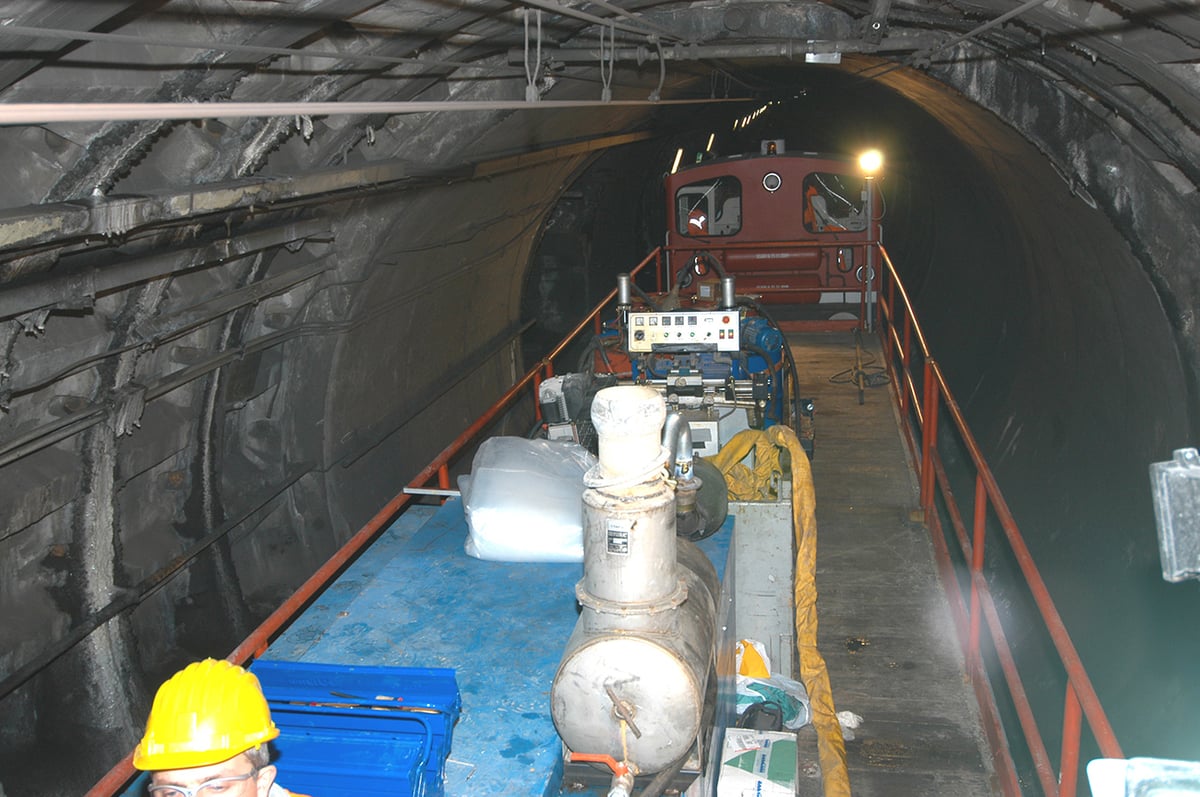
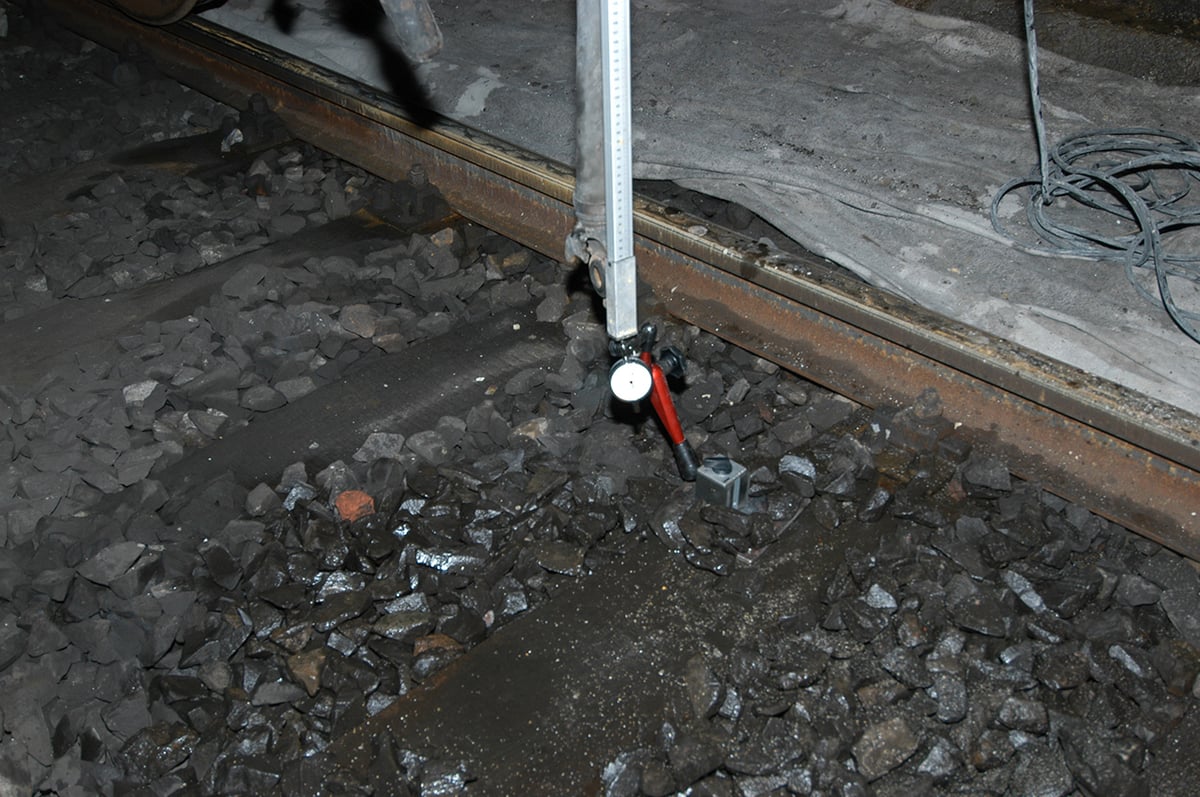
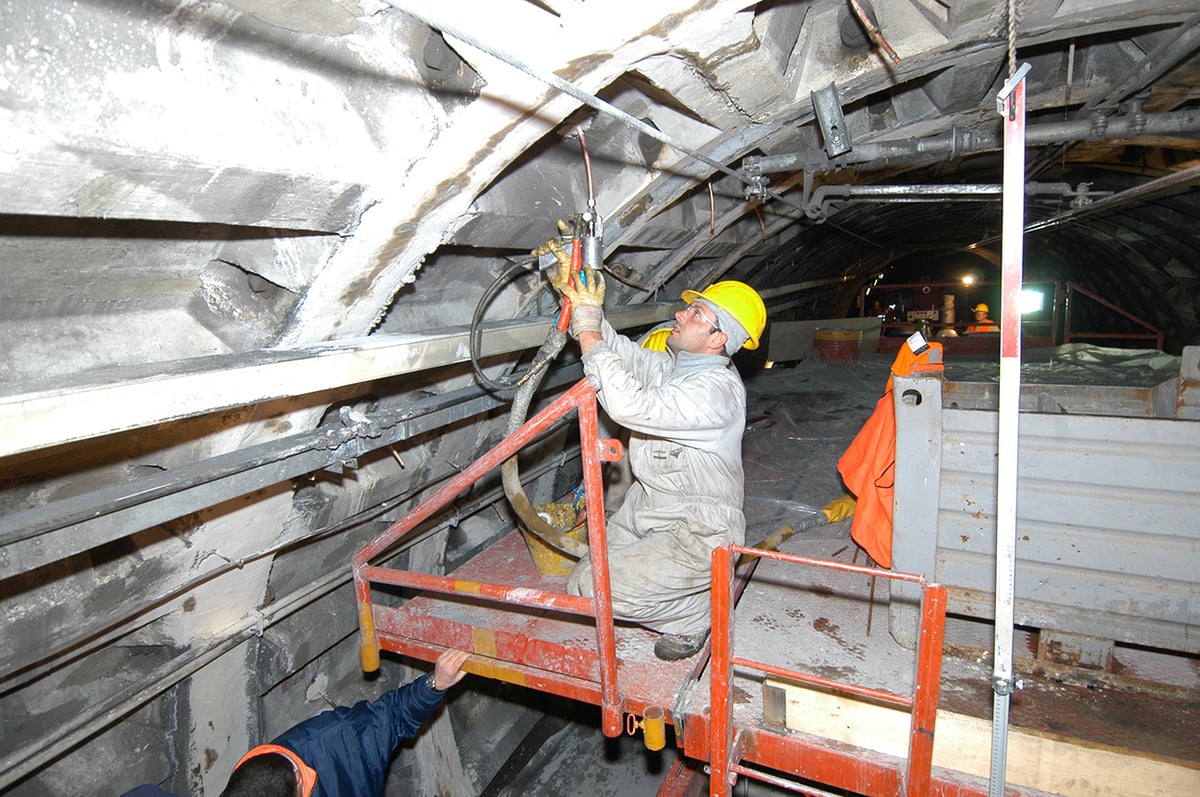