The historical Monfalcone shipyard produces high-tonnage ships for the world’s largest cruise operators. It covers a surface area of 787,000 square metres and is the largest in the Fincantieri group.
THE PROBLEM
The continuous transit of cranes and other heavy vehicles over time led to the differential subsidence of the foundation soil under the strip of industrial pavement made of reinforced concrete located between the service area and the overhead crane rail in the ship assembly area. The deformed area along the cable channel had widespread irregular dips, with subsidence up to 60 mm. This subsidence made the paving unsuitable for supporting the weight of cranes transporting heavy loads, representing a danger for workers in the area.
Customer needs
Fincantieri could not plan for prolonged work stoppages, so it was necessary to intervene quickly and minimize the impact on shipyard activities. It also had to fully protect the safety of personnel and guarantee long-term effectiveness of the consolidation work.
Why Fincantieri chose Uretek:
- Speed
Careful planning and programming of the times allowed the work to be completed in just two days; - Non-invasive
The intervention proposed by Uretek did not require excavations or masonry work, and it did not dirty the area or produce waste; - Localized work
The Uretek team delimited the work area, allowing regular Fincantieri activities to continue; - Continuous monitoring of the work
Both during and after the intervention, the activities were subject to control by highly qualified personnel using advanced laser technology; - Exclusive Uretek technology
The intervention involved the injection of Uretek Geoplus® resin. With its high swelling pressure, it compacts the soil and stabilizes structures; - Respect for the environment
Above-ground mixing of the Uretek® resin creates a final inert product that does not release solvents into the soil or possible water tables in the area; - Insurance and contract guarantee
10 years.
THE SOLUTION
The deformed area consisted of underlying granular soil that had not been compacted when the service area was built. The Uretek intervention involved injections of Geoplus® resin with rapid expansion and high swelling pressure, which thickened the deep soil in the entire area surrounding the injection point. In this way, contact between the subgrade and reinforced concrete curb was completely restored. The intervention involved 3 different areas where the bridge crane passed, for a total of about 80 ml of kerb.
The resin injections were monitored constantly using an analogue centesimal comparator and a work-site laser level, which provided a real-time view of the behaviour of the kerb and surrounding paving with respect to the vertical movement. The four comparative dynamic penetration tests showed the success of the intervention, given the increase in mechanical parameters of the volumes of soil treated with injections.
THE INTERVENTION IN DETAIL
The soil underneath the channel-bearing kerb is granular fill mixed with clay, deposited alongside the support structure for the bridge crane that was built many years before. During the last work on the service area in 2008/9, the underlying fill was compacted and the 40-cm-thick floor was poured, but the soil of the existing adjacent strip could not be compacted.
The injection holes were drilled by means of electric roto-percussion hand drills. In this phase, the kerb surface was surveyed at a depth of about 0.60–0.80 m below the work surface.
Holes with a diameter of 26 mm were drilled through the reinforced concrete kerb, extending at some points to a maximum of 2.0 m below the thickness of the kerb. These were spaced at regular intervals, working from above and in the centre of the channel. Once drilling was complete, the steel injection ducts were inserted by percussion. The injections were first made in the upper levels and then deeper, at a depth of 0.10 m and 1.10 m from the kerb surface. At critical points where the carrier wheels pass, a third injection level was created at a depth of about 2.00 m below the surface. In this way, the entire precise volume of so-called ‘significant’ terrain was reached and consolidated.
Observations
The vertical lift of the concrete structure attests to the effectiveness of the treatment. In fact, this can only occur after the expansion of the swelling resin has thickened all the soil surrounding the injection site in directions other than vertical.
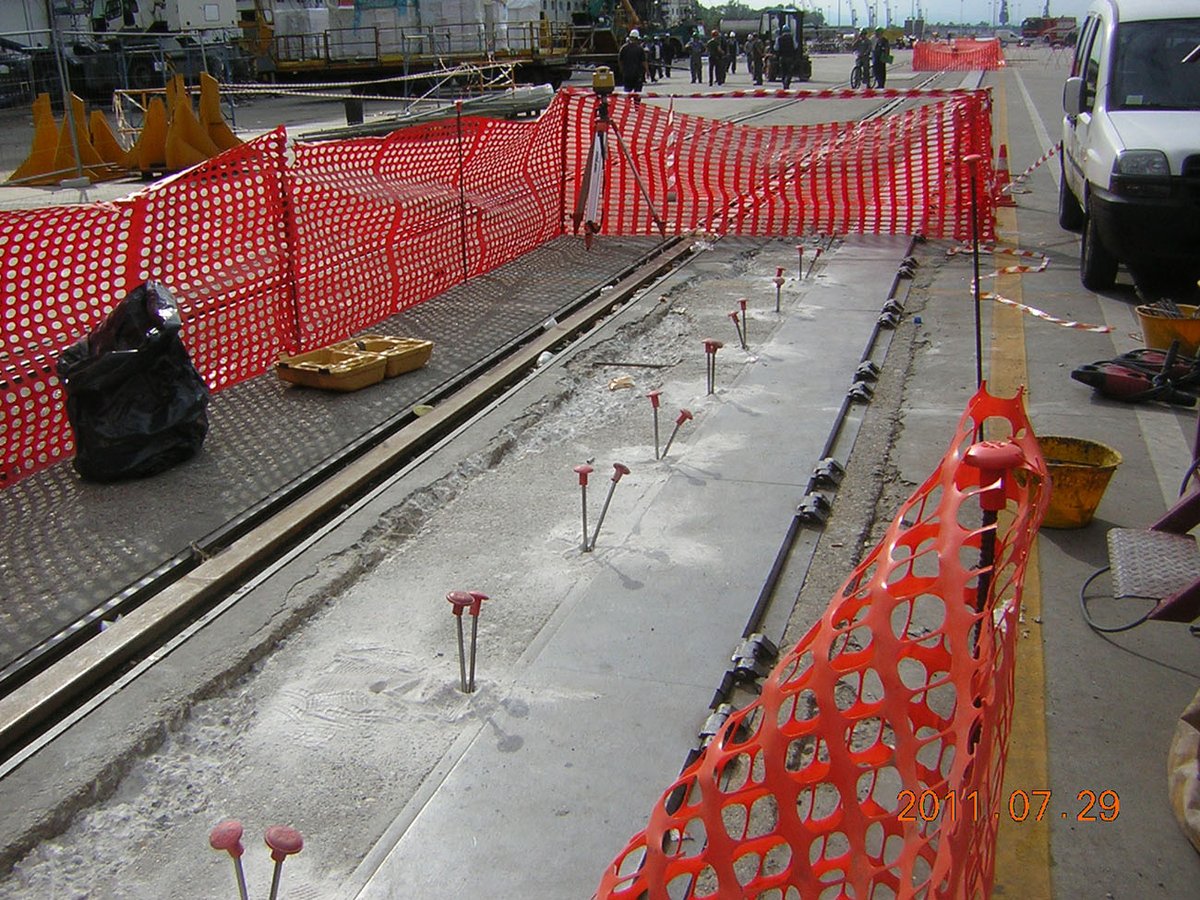
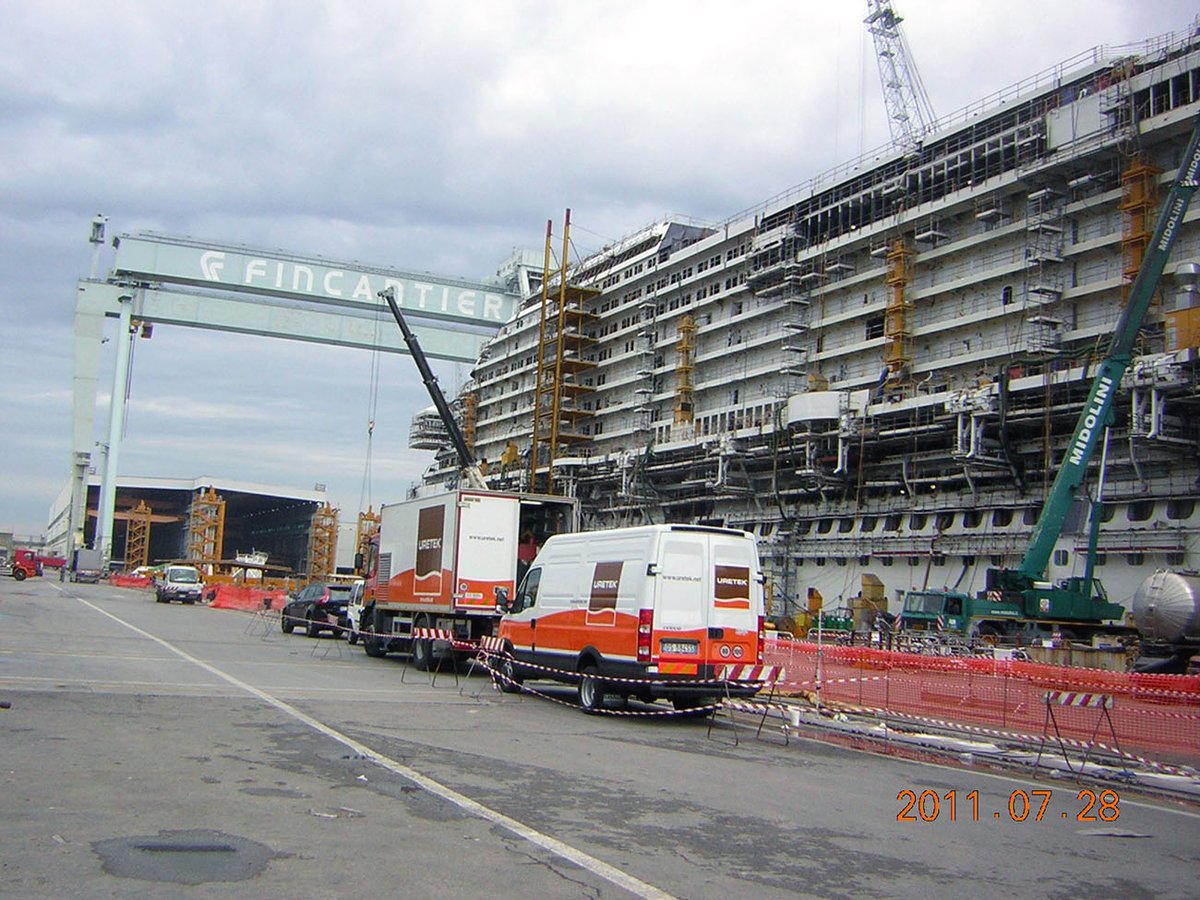
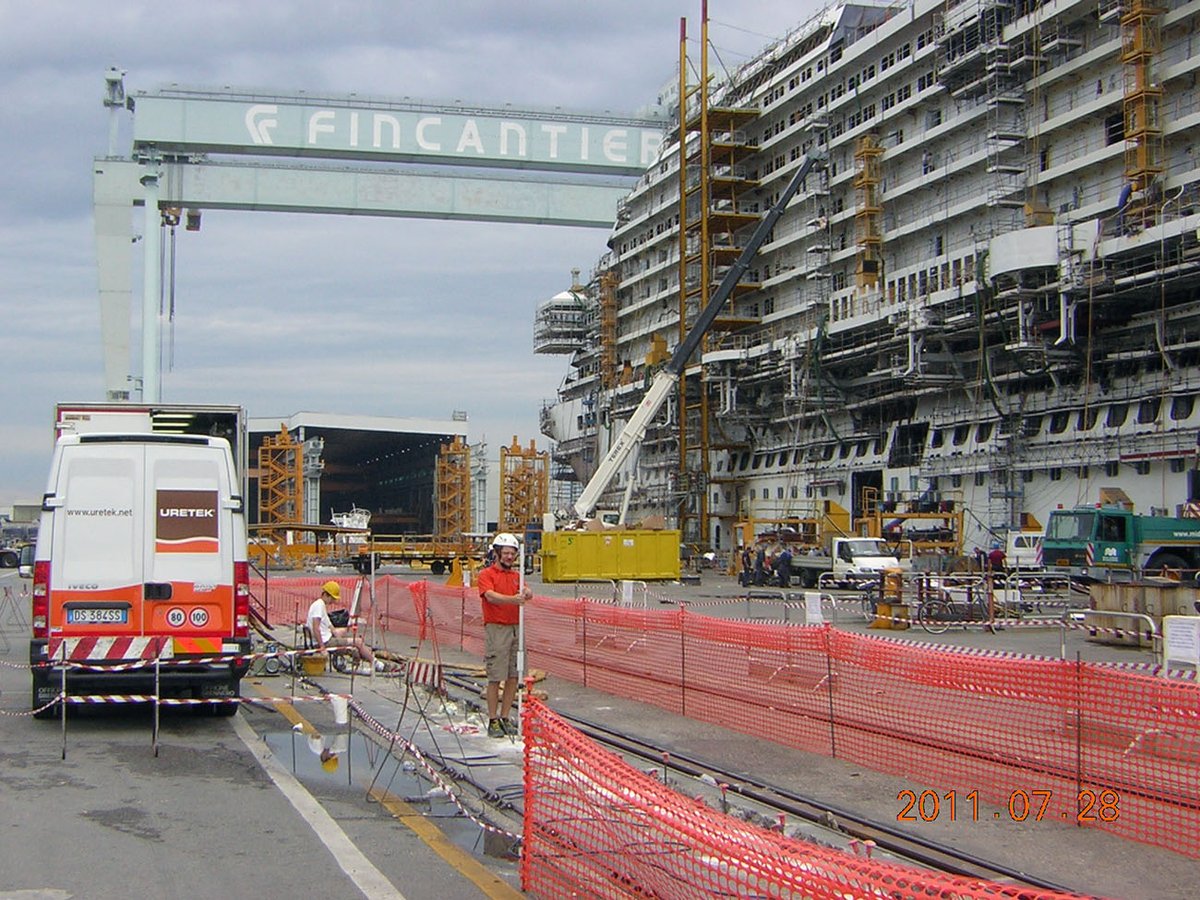
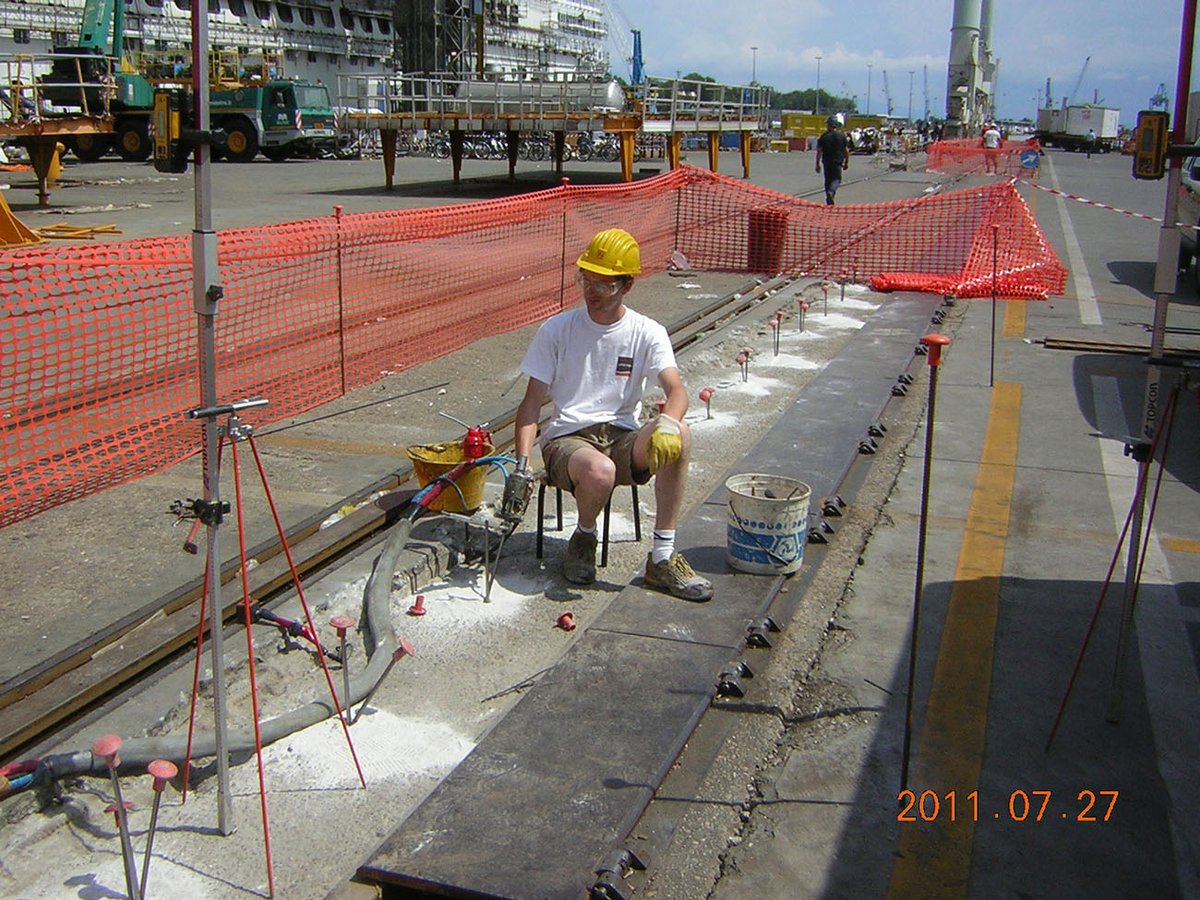
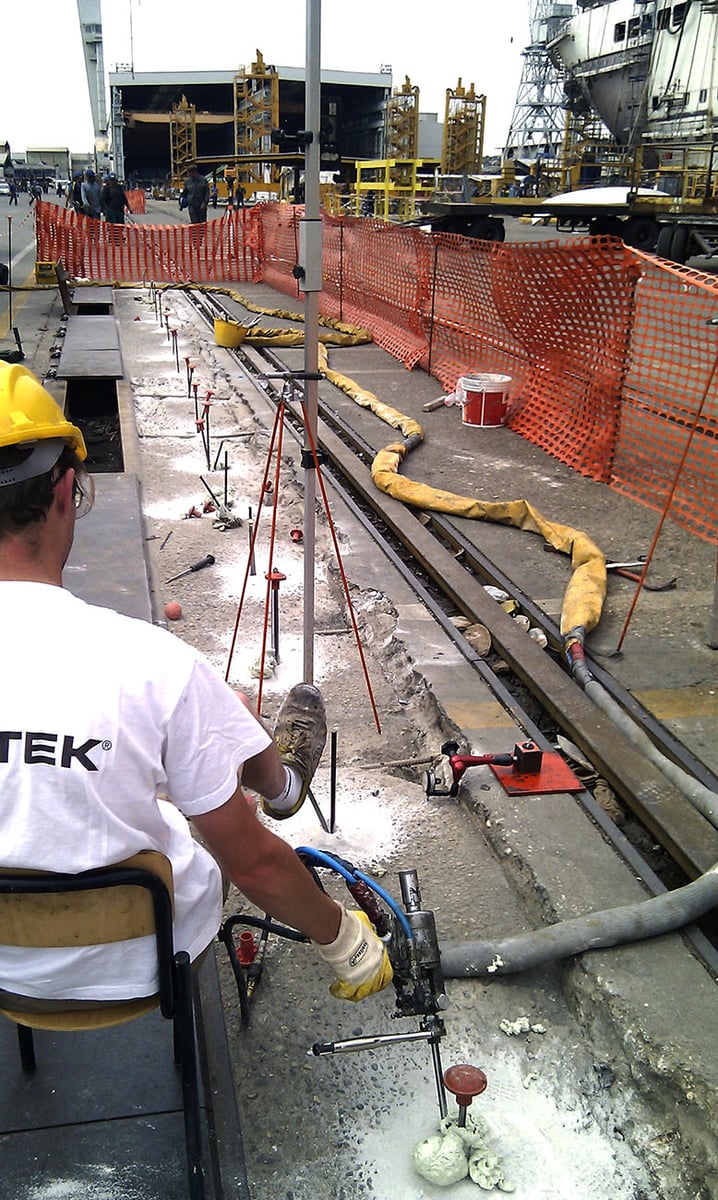
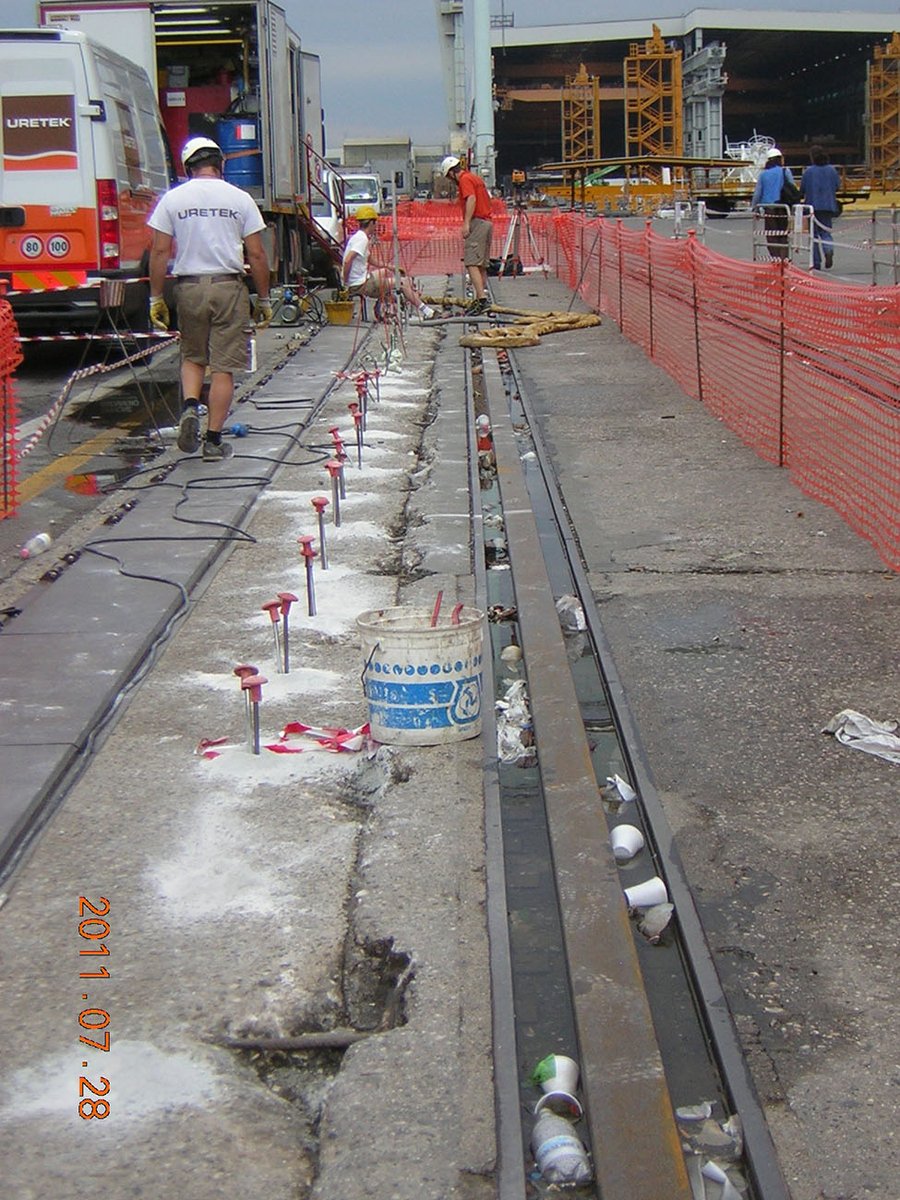
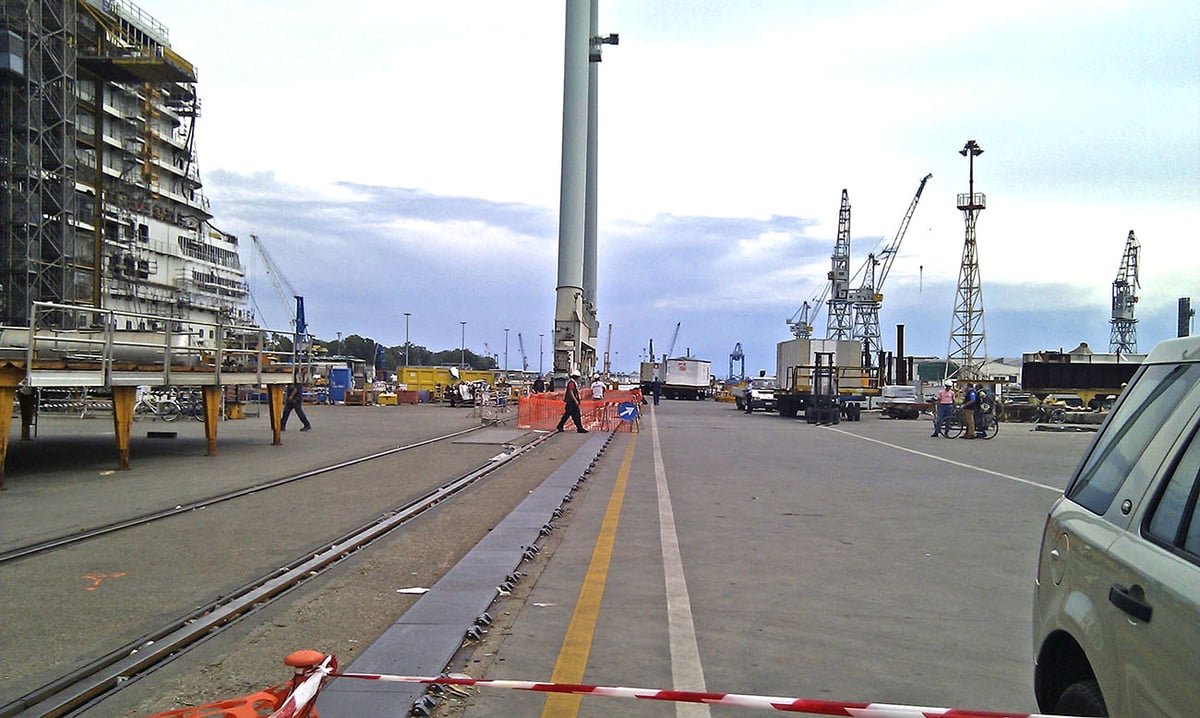
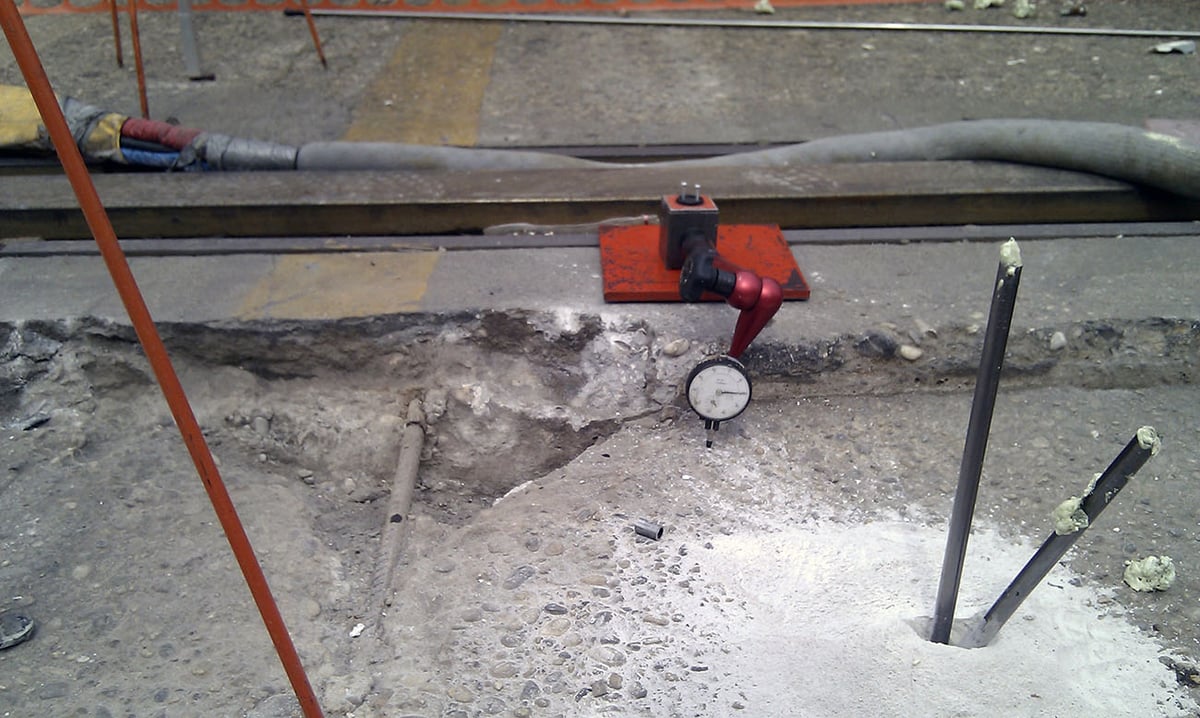