The section of provincial road 413 runs parallel to the A22 Brennero motorway and connects the city of Modena with Carpi and Novi di Modena, continuing on towards Mantua. Traffic is rather intense, with many heavy vehicles.
THE PROBLEM
The road paving in the section between km 38.200 and km 41 showed dangerous dips and even large longitudinal fissures. The subsidence was attributed to compaction of the fill on which the paving was laid, accentuated by the vibrations of passing heavy vehicles and subsequent operations to regenerate the road surface, which had reached a thickness of 1 metre at some points.
Customer needs
The customer needed a decisive intervention that would guarantee the utmost safety in the long term. It also could not interrupt normal traffic. Given the importance of the artery, blocking traffic would have caused not only enormous inconvenience, but also notable damage to the entire local economy.
Why the Uretek solution was chosen:
- Speed
Careful planning and programming of the times allowed the work to be completed in a relatively short time; - Competitive prices
- Non-invasive
The intervention proposed by Uretek did not require excavations or masonry work, and it did not dirty the area or produce waste; - Continuous monitoring of the work
Both during and after the intervention, the activities were subject to real-time control by highly qualified personnel using advanced laser technology; - Application of the exclusive Uretek Deep Injections® technology
With the Uretek Geoplus® expanding resin with high swelling pressure, the soil is compacted and the structures stabilized; - Respect for the environment
Above-ground mixing of the Uretek® resin creates a final inert product that does not release solvents into the soil or possible water tables in the area.
THE SOLUTION
None of the numerous interventions made in the past by ANAS (sheet piling, bentonite piles, lime stabilization, etc.) had led to significant improvements. Therefore, technicians in the Province of Modena decided to adopt an innovative technology: injections of polyurethane resins with a high swelling pressure. Expanding, they compact the solid volume, with the consequent increase in load-bearing capacity. Uretek Deep Injections®, our flexible and non-invasive technology allowed us to meet the client’s needs without removing the road surface and without blocking traffic.
The final investigations showed that the strength and deformability parameters of the treated soil improved substantially. All vertical axes investigated with penetration tests, both static and dynamic, showed an increase in tip resistance compared to the pre-intervention reading of more than 40% (as predicted by the project) and between 80% and 100% on average. We carried out the work within the times established in the work programme: 35 days.
THE INTERVENTION IN DETAIL
The work site
For technical reasons and to protect exclusive rights, the project was assigned to Uretek via a negotiating procedure in compliance with Art. 57, Section 2, Letter b of Legislative Decree 163/2006.
The intervention concerned a section of about 2.8 km of provincial road in which we made a total of 10,700 injections covering a total surface area of 17,400 sq. m.
Work site planning
We organized the work site to guarantee the alternating one-way flow of traffic on an entire lane of provincial road 413 regulated by a traffic signal. We carried out the work in three eight-hour shifts in teams of eight people per shift, five days a week, 24 hours a day. Each team consisted of a signalling manager, a work-site head, two workers assigned to drilling and two to injections, a team leader, and an assistant. Two fully equipped shop trucks were present at the site, one as a spare, a caravan for use as an office, and three lights used during the night shifts.
SUMMARY
- 2.8 km of road (one lane) in each direction;
- about 18,000 m2 of road surface area;
- 10,700 holes drilled with a spacing of 1.25 m; 3 teams, each composed of 7–8 people in 8-hour shifts;
- 35 days, 5 days per week, 24 hours per day;
- numerous verifications: penetration and static tests, pressure tests, and seismic tests;
- 70 m maximum work-site length; 60 seconds maximum wait at the traffic light.
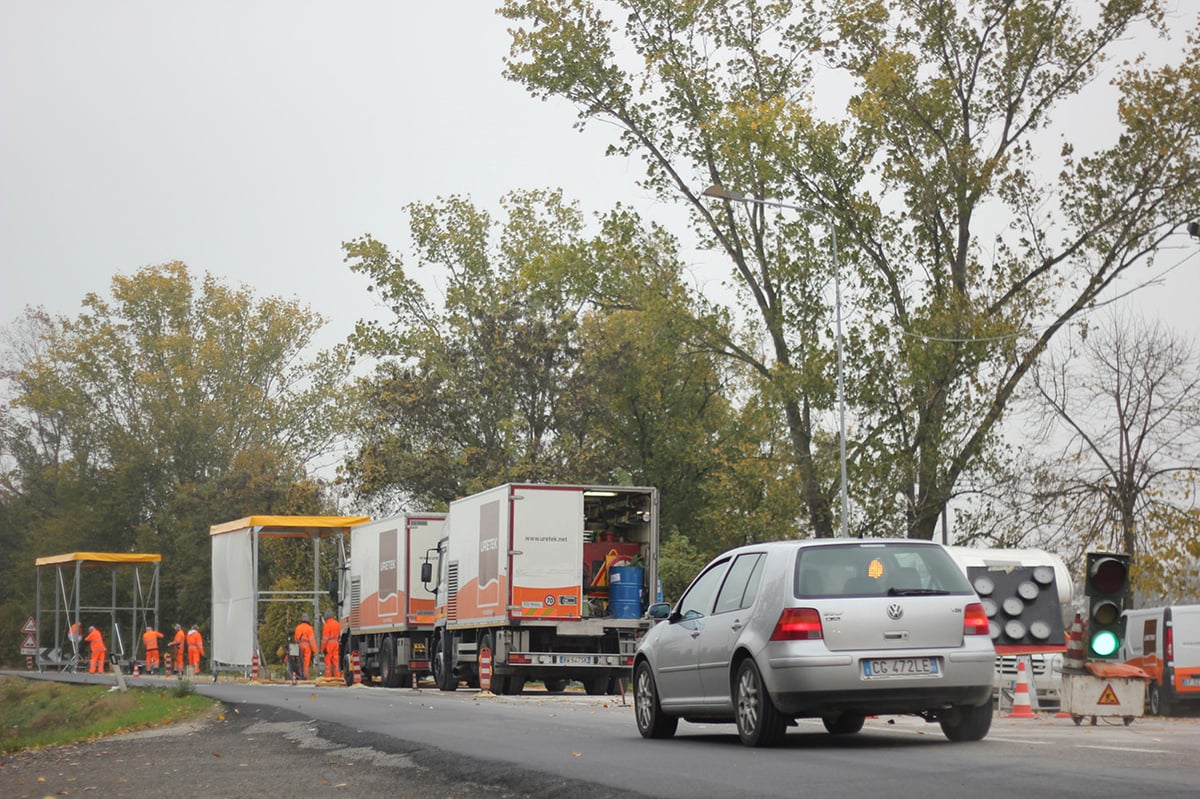
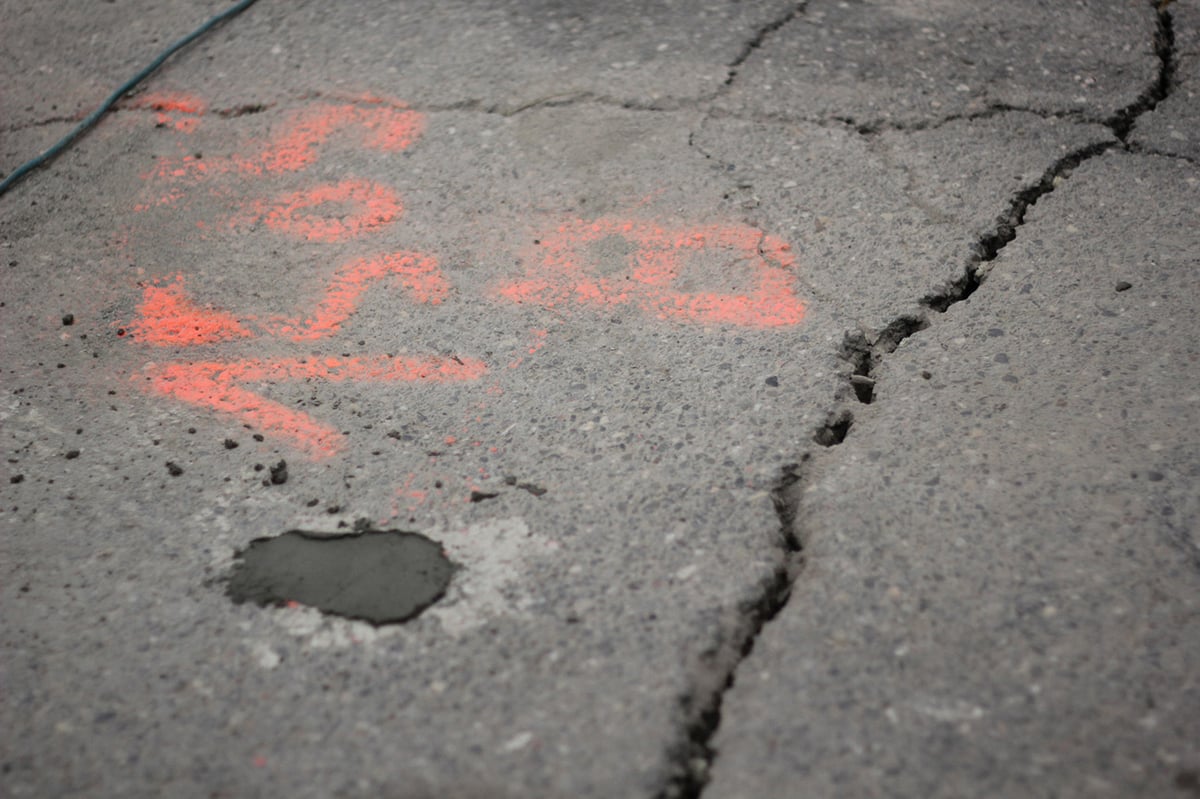
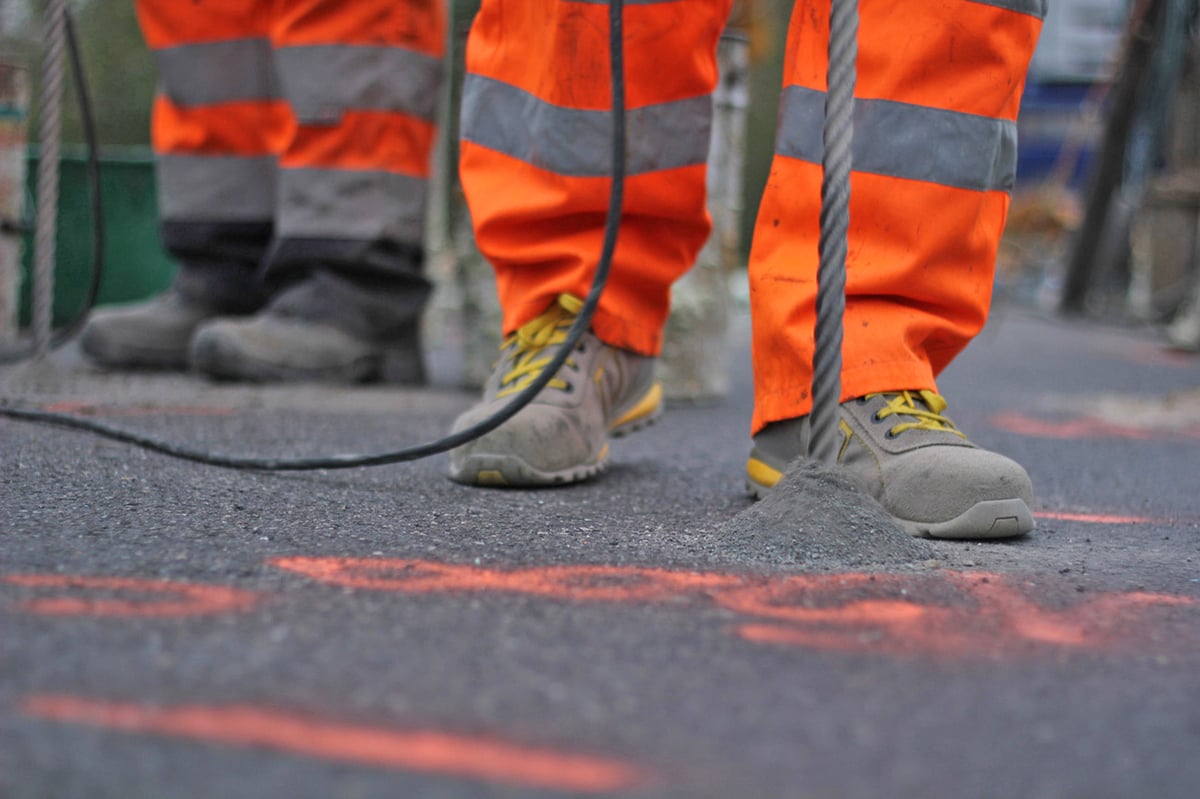
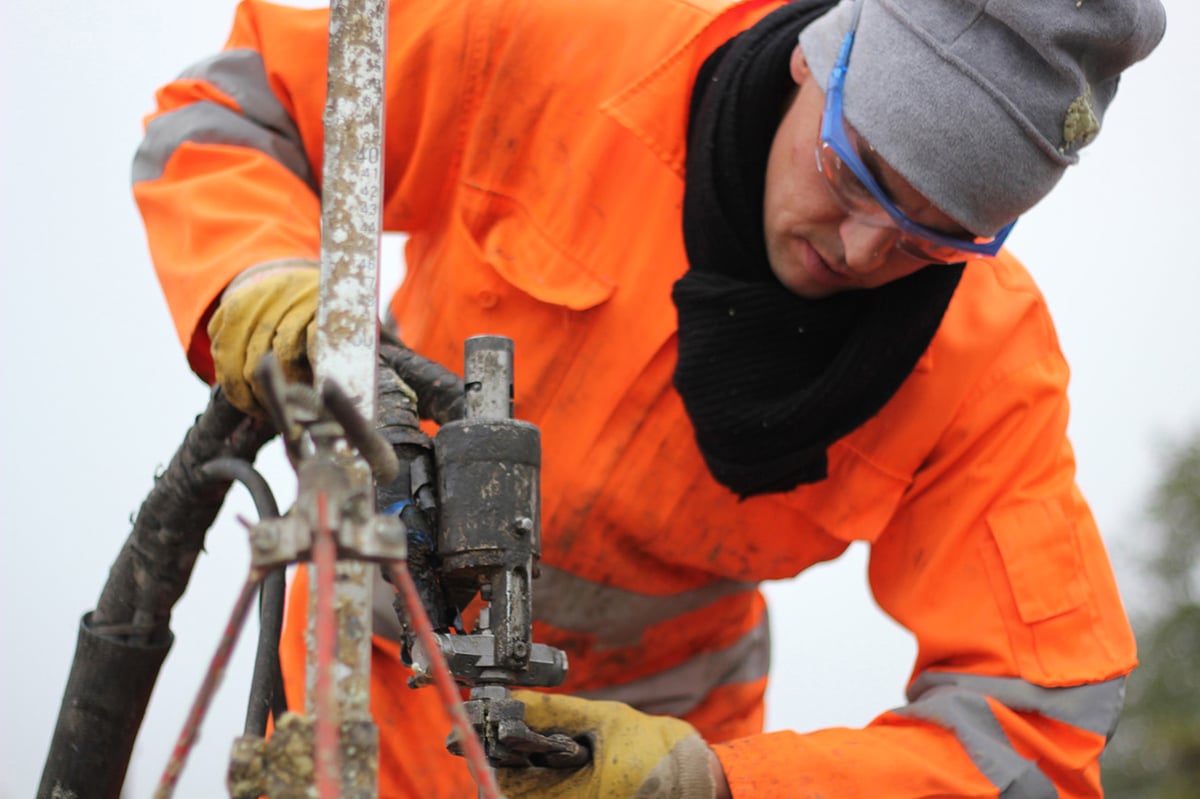
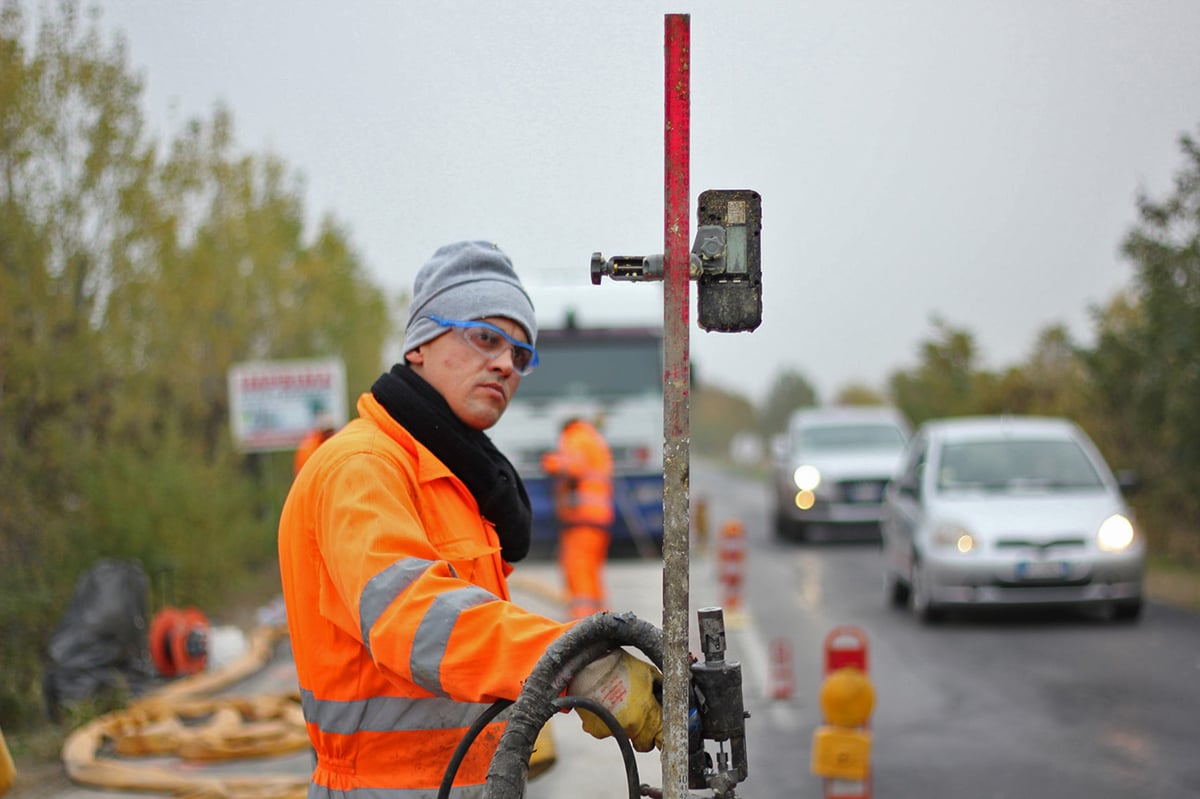
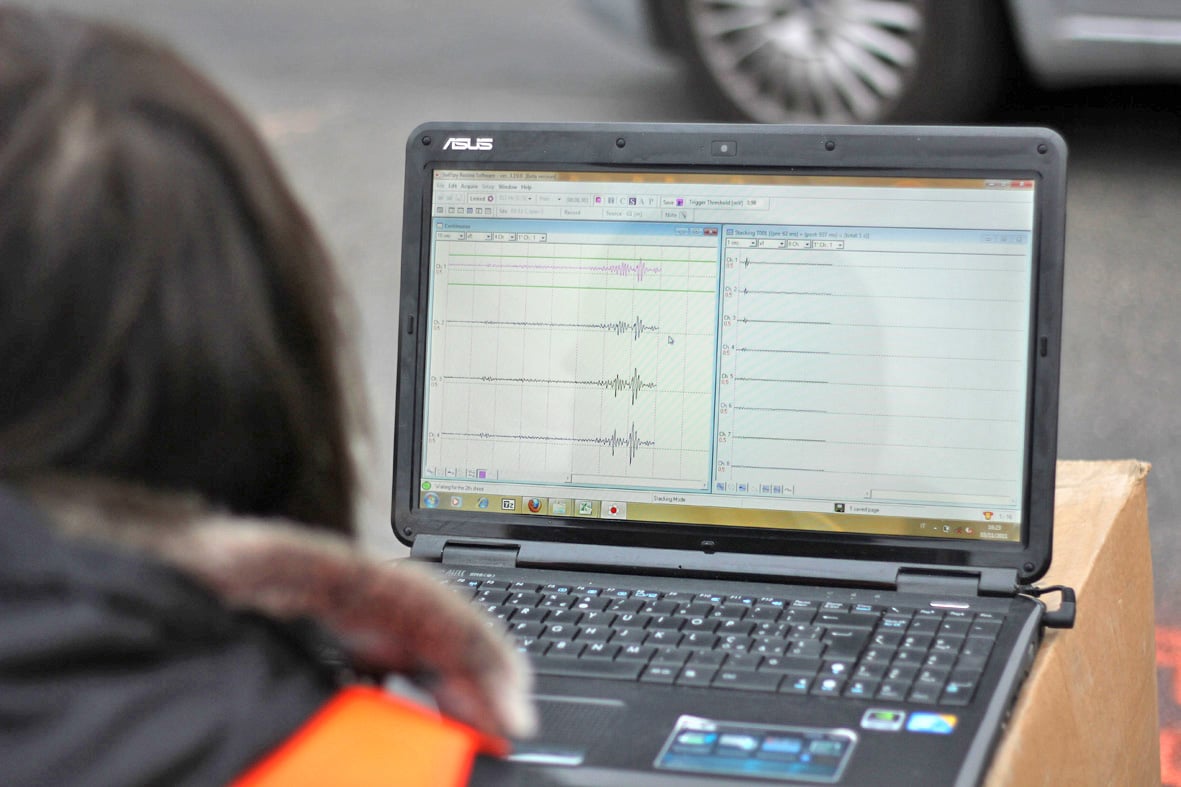
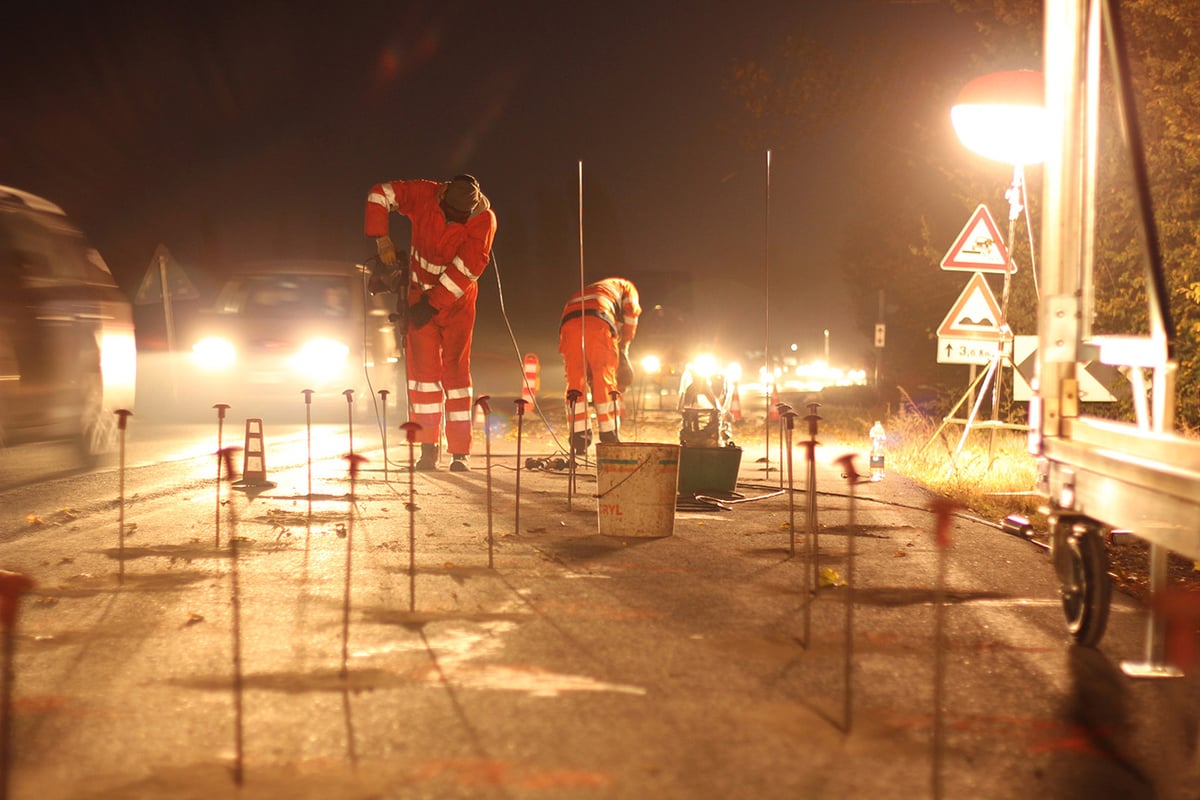
Operational phases
We first traced the grid of holes and associated a progressive number to each hole for each direction in the work site. Using handheld drills, we made holes in the layer of asphalt to the depth of the extrados of the underlying embankment. We then inserted injection tubes into the soil down to a depth of 4 metres below the road surface and injected the two-component expanding resin with a specific gun. During the injections, we started from the deepest part and rose to the height of the intrados of the asphalt layer, progressively extracting the injection tube using a hydraulic extractor at a controlled speed. For each injection (identified by the assigned number), we recorded the total amount of resin injected and constantly controlled the height of the road surface using a laser level in order to stop the injection in the event of abnormal swelling. Following the injection, we fully extracted the tube and sealed the hole with a suitable mortar.
Watch the video of the intervention